- INFO POINT
- Di Silvano Lova
- Cosa: Struttura 1
La collaborazione tra l’azienda modenese WamGroup e l’università di Brescia testimonia che ghiaia, sabbia e acqua, dopo il trattamento Consep System, possono essere reimpiegati per produrre nuovo calcestruzzo
Economia circolare e settore delle costruzioni. Un matrimonio che s’ha da fare. In primo luogo perché questa è la direzione cui deve tendere l’economia mondiale. Secondo perché nel nostro Paese, ogni anno, per realizzare case, strade, ponti, ferrovie, vengono estratti 29 milioni di metri cubi di sabbia, ghiaia e materiali naturali. In questo contesto, la filiera del calcestruzzo può svolgere un ruolo importante, per una rapida conversione del settore verso la circolarità. Gli aggregati riciclati, in sostituzione di quelli naturali, possono infatti offrire un contributo prezioso.
Il valore del riciclo
Utilizzando materie prime riciclate è possibile risparmiare 15 milioni di tonnellate di aggregati naturali
Una tesi, questa, sostenuta dalla stessa Federbeton che, dati alla mano, dimostra che ogni anno è possibile risparmiare oltre 15 milioni di tonnellate di aggregati naturali su un totale di 28 milioni di metri cubi di calcestruzzo prodotto (il dato si riferisce al 2019 e il tasso medio di sostituzione delle materie prime vergini con quelle di recupero è calcolato al 30%; nda).
Si tratta di cifre enormi, che aiutano a capire quanto siano significative le potenzialità della filiera.
Il calcestruzzo di risulta
Tra le possibili fonti di materiali alternativi agli aggregati naturali vi sono i prodotti ottenuti dal trattamento del calcestruzzo di risulta (o reso o di ritorno), ovvero il calcestruzzo fresco che, per vari motivi, non viene utilizzato interamente in cantiere e a fine giornata torna, con l’autobetoniera, all’impianto di produzione.
In assenza di dati ufficiali relativi all’effettiva quantità prodotta di calcestruzzo reso, si stima che, nei paesi europei, esso rappresenti circa il 2-3% dell'intera produzione di calcestruzzo. Ciò significa che in Italia, ogni anno, circa 700mila metri cubi di calcestruzzo non vengono utilizzati, tornano agli impianti di produzione e diventano rifiuto da smaltire.
Appare evidente che l’implementazione di sistemi di trattamento e recupero di tale materiale di risulta garantirebbe una minore necessità di utilizzo e reperimento di materie prime vergini, con la riduzione delle pressioni ambientali sulle risorse naturali.
Dal trattamento della “risulta” è possibile ottenere nuovi prodotti, che possono essere nuovamente utilizzati nel confezionamento di nuovo calcestruzzo.
In particolare, grazie a impianti tecnologicamente innovativi, è possibile recuperare aggregati fini (sabbia), aggregati grossolani (ghiaia), acqua microfiltrata e polvere di cemento.
Se il 3% sembra poco
Ogni anno il 3% del calcestruzzo prodotto non viene utilizzato e diventa rifiuto da smaltire, parliamo di 700.000 metri cubi
La collaborazione WamGroup e università di Brescia
Chi sta lavorando all’obiettivo di recuperare il calcestruzzo di ritorno e di reimmetterlo per produrre nuovo calcestruzzo è l’azienda modenese Wamgroup che, attraverso il sistema di trattamento combinato Consep System, è in grado di dare nuova vita alle componenti della miscela di calcestruzzo, recuperando importanti quantità di materiale inerte e acqua.
Coerentemente con le normative tecniche di settore, tali prodotti - aggregati, acqua microfiltrata e fango di cemento -, come nuove materie prime per la produzione di calcestruzzo, devono sottostare a determinati requisiti tecnici e ambientali, al fine di assicurare, contemporaneamente, la salvaguardia dell’ambiente e adeguate prestazioni meccaniche.
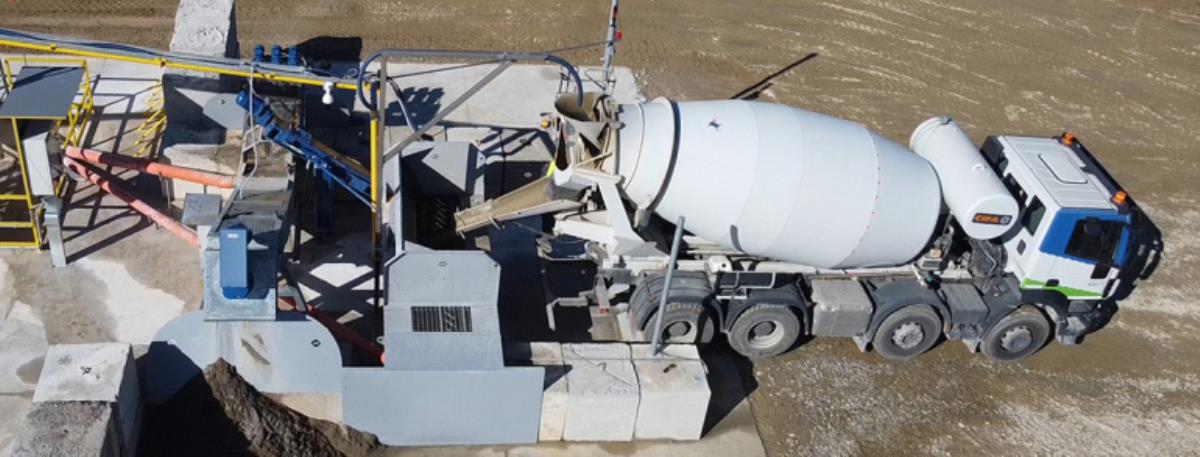
Per questo scopo, WamGroup e il dipartimento di Ingegneria civile, ambiente, territorio, architettura e matematica dell’università degli Studi di Brescia hanno collaborato a uno studio dal titolo “Recupero di materia dal calcestruzzo di risulta derivante dal lavaggio delle betoniere”.
L’obiettivo principale era approfondire le prestazioni tecniche e ambientali dei prodotti ottenuti dal trattamento del calcestruzzo di risulta, nonché la fattibilità e l’idoneità per produrne di nuovo.
Contemporaneamente è stata valutata e valorizzata l’efficienza degli impianti dell’azienda modenese nella “pulizia” dell’acqua di lavaggio e degli inerti di distinta dimensione, evidenziandone il raggiungimento degli standard normativi per il recupero nel settore delle costruzioni.
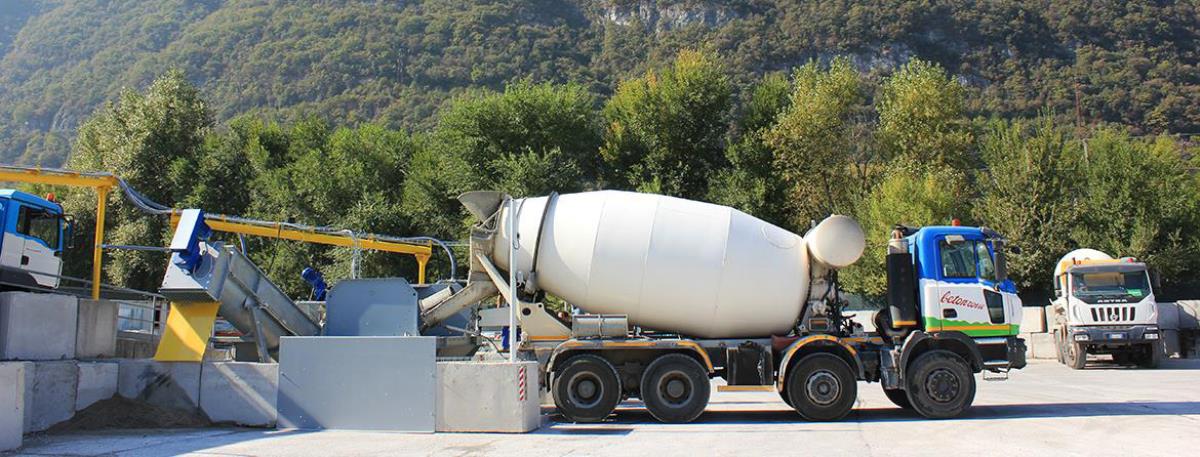
L’analisi sperimentale è stata sviluppata, in via preliminare, su due impianti localizzati in due centrali di betonaggio con sedi a Mirandola, vicino a Modena, e Lavis, in provincia di Trento. In una seconda fase, lo studio è stato focalizzato solo sull’impianto trentino, sul quale sono state eseguite prove di caratterizzazione completa delle componenti recuperate.
La tecnologia Consep System
L’impianto di trattamento del calcestruzzo di risulta implementato dall’azienda Wamgroup si compone di due sezioni principali. La prima è Consep, e serve a recuperare la frazione inerte presente nel calcestruzzo di risulta. Il processo, tramite un sistema meccanico dotato di buffer e coclee alimentatrici, permette di recuperare aggregati fini (sabbia) con diametro delle particelle inferiore a 5 millimetri e aggregati grossolani (ghiaia) con diametro delle particelle superiore a 5 millimetri. Inoltre, durante la fase di separazione e vagliatura, ciascuna frazione granulometrica viene perfettamente lavata tramite un sistema di ugelli spruzzatori.
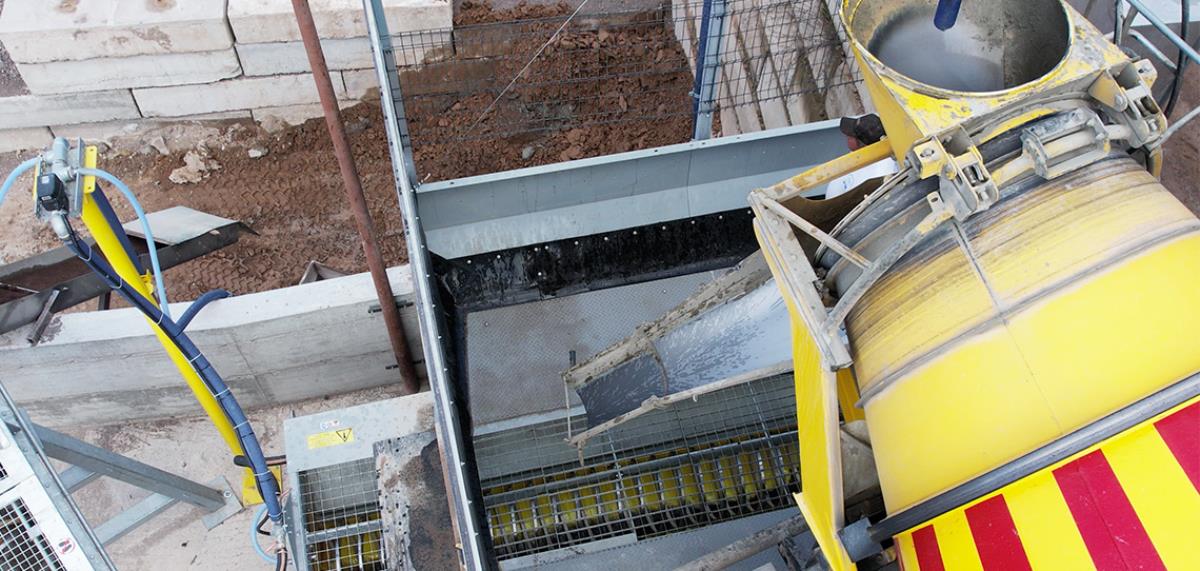
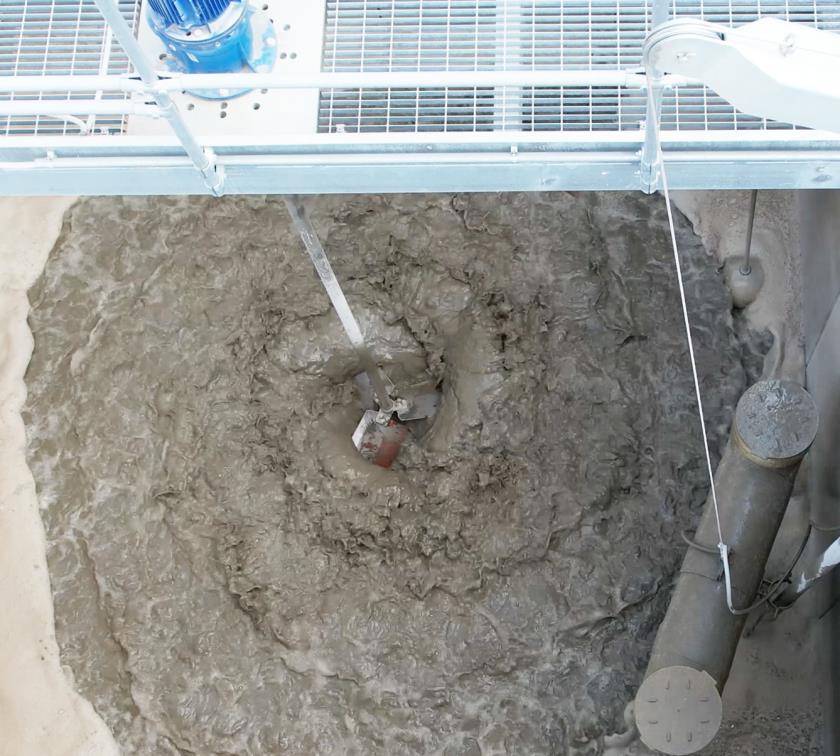
L’acqua di lavaggio (che comprende l’acqua utilizzata per il lavaggio dell’autobetoniera prima dello scarico del calcestruzzo reso nel buffer e l’acqua di risulta derivante dal lavaggio degli inerti) viene trasportata all’interno di una vasca di accumulo e, successivamente, inviata al processo di microfiltrazione Hyfil.
La seconda sezione si chiama appunto Hyfil e serve a trattare l’acqua di lavaggio (acqua più cemento) con conseguente recupero dell’acqua chiarificata e fango di cemento. L’acqua di lavaggio proveniente dal lavaggio dell’autobetoniera e della frazione inerte viene conferita, in prima fase, a una vasca di accumulo e mantenuta in agitazione tramite agitatori meccanici, al fine di impedire la sedimentazione dei solidi sospesi presenti al suo interno.
Tramite una pompa sommersa l’acqua viene successivamente inviata al processo di microfiltrazione che, attraverso l’utilizzo di una membrana filtrante, permette la separazione della fase liquida (acqua microfiltrata) dalla fase solida (fango di cemento). L’acqua microfiltrata viene successivamente mandata a un serbatoio di raccolta, mentre il fango di cemento viene scaricato tramite coclea in un’area di stoccaggio dedicata.
La sperimentazione
Durante lo studio è stato sviluppato un approfondimento sperimentale finalizzato alla valutazione delle prestazioni tecniche e ambientali dei prodotti ottenuti dal processo di trattamento, nonché delle prestazioni meccaniche del calcestruzzo confezionato con tali materiali.
In particolare, la frazione inerte composta da aggregati fini (d = 5 mm) e aggregati grossolani (d = 5 mm) è stata sottoposta, in accordo ai requisiti richiesti dalla norma tecnica di settore (UNI EN 12620 “Aggregati per calcestruzzo”), alle seguenti prove di caratterizzazione: analisi granulometrica, equivalente in sabbia, blu di metilene, massa volumica in mucchio e del granulo, assorbimento d’acqua, reattività alcali-silice, contenuto di cloruri idrosolubili, solfati solubili in acido, contenuto di zolfo totale, descrizione petrografica, impurezze organiche leggere, prova di radioattività e, infine, test di cessione (UNI EN 12457-2).
Viceversa, l’acqua di lavaggio (prima e dopo la microfiltrazione) è stata sottoposta alla valutazione del contenuto di solidi sospesi totali e, contemporaneamente, alle prove di caratterizzazione richieste dalla norma UNI EN 1008 “Acqua d'impasto per il calcestruzzo”; ciò al fine di valutare l’idoneità dell’acqua microfiltrata per la produzione di nuovo calcestruzzo. Sul fango di cemento sono state invece eseguite prove di valutazione del contenuto di sostanza secca e umidità, nonché prove atte a identificare eventuali capacità residue del calore di idratazione (metodo della calorimetria a conduzione isotermica UNI 196-11).
Calcestruzzi nuovi, aggregati riciclati
La sperimentazione ha previsto il confronto fra calcestruzzi realizzati con il 100% di aggregati vergini e miscele con il 50% di aggregati
Infine, l’attività ha previsto anche il confezionamento di miscele di calcestruzzo con classi di resistenza C10/15, C25/30 e C30/37 utilizzando aggregati, acqua microfiltrata e fango di cemento provenienti dal calcestruzzo di risulta, in combinazione con aggregati naturali e acqua microfiltrata. In particolare, sono state prodotte le seguenti miscele: miscela “riferimento” (100% di aggregati naturali - 100% di acqua naturale); miscela “50%-riciclato” (50% di aggregati provenienti da calcestruzzo di risulta e 50% di aggregati naturali - 50% di acqua naturale e 50% di acqua microfiltrata); miscela “fango” (stessa miscela precedente - 50%-riciclato - con la sostituzione di 50 kg/mc di sabbia con 50 kg/mc di fango di cemento). Le miscele sono state successivamente sottoposte a test di compressione dopo 28 giorni di maturazione in camera nebbia a temperatura di 20°C e umidità relativa = 95%, in accordo alla norma UNI EN 12390-3 (“Prova su calcestruzzo indurito: resistenza a compressione dei provini”).
I risultati della ricerca sperimentale
I risultati finali ottenuti hanno evidenziato che, in termini di proprietà geometriche, fisiche e chimiche, gli aggregati soddisfano i requisiti imposti dalla norma UNI EN 12620 e dalla sua applicativa UNI 8520-2, risultando, pertanto, idonei alla produzione di nuovo calcestruzzo.
In particolare, tra le principali caratteristiche, si evidenziano valori di massa volumica in condizioni di superficie satura asciutta pari a 2.660 kg/mc per l’aggregato fine e 2.720 kg/mc per l’aggregato grossolano (valori che rispettano ampiamente il limite normativo minimo di 2.300 kg/mc).
In termini di assorbimento d’acqua, l’aggregato grossolano presenta un valore percentuale pari allo 0,9% che, anche in questo caso, rispetta il limite normativo massimo dell’1% richiesto per il confezionamento di calcestruzzi operanti in classe di esposizione Xf.
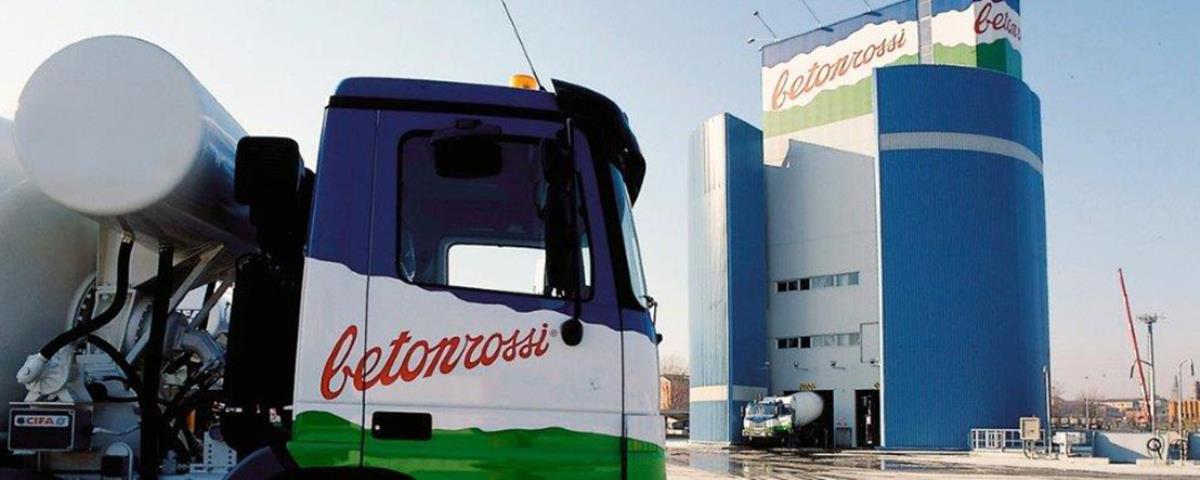
Relativamente agli aspetti ambientali, i risultati ottenuti dal test di cessione, eseguito in accordo alla metodica UNI EN 12457-2 (dmax = 4 mm; L/S = 10 L/kg; tempo di contatto 24 ore; acqua demineralizzata), non hanno evidenziato alcun rilascio di sostanze inquinanti nell’ambiente, se non un valore alcalino di pH dell’eluato (nell’intervallo 10-12), ma sempre inferiore al limite normativo imposto dal decreto ministeriale 186/2006. Anche l’acqua microfiltrata risulta idonea alla produzione di nuovo calcestruzzo. In particolare, sono soddisfatti tutti i requisiti prestazionali richiesti dalla UNI EN 1008, sia in termini di tempo di inizio-fine presa che di resistenza a compressione dei provini di malta confezionati con l’acqua in esame. Va detto che anche i requisiti chimici imposti dalla sopracitata normativa vengono ampiamente soddisfatti. In particolare, l’acqua soddisfa sia i requisiti di pH, che si attesta a un valore pari a 12,8 (valore minimo ammesso dalla normativa pari a 4), che quelli relativi al contenuto di ioni cloruro e al contenuto di solfati.
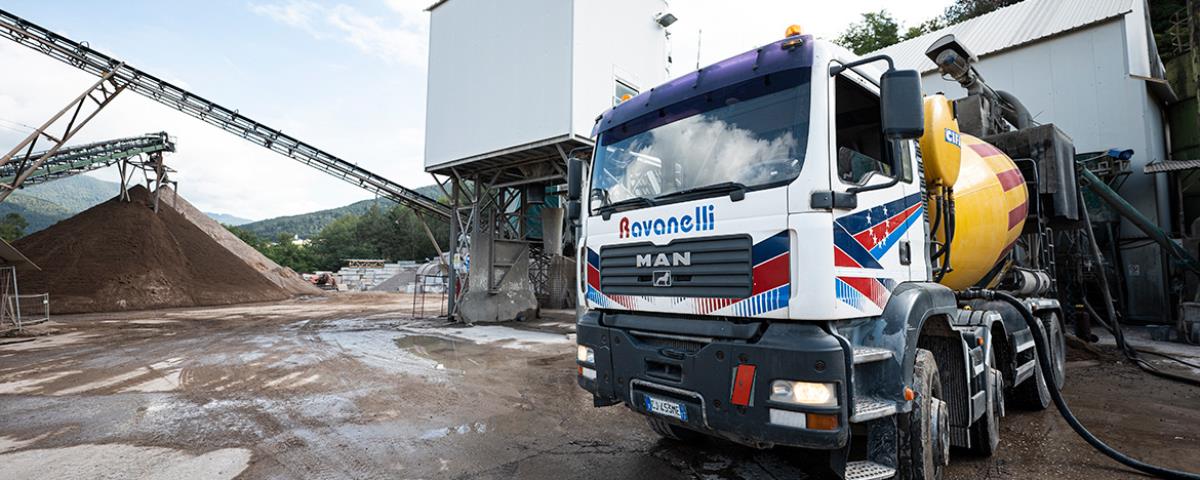
Tale limitazione, in particolare nel contenuto di cloruri e solfati, è di fondamentale importanza poiché finalizzata a impedire la formazione di espansioni e fessurazioni del calcestruzzo (solfati), nonché la corrosione delle armature (cloruri).
Dalla valutazione del contenuto di solidi sospesi totali, calcolato su campioni di acqua di lavaggio prima e dopo il processo di microfiltrazione, è emerso che, nel campione in ingresso (acqua sporca prima della microfiltrazione), il contenuto di solidi sospesi, nonché di sostanza secca, varia in un intervallo percentuale di circa l’8-9,7% sul volume totale.
Al contrario, il permeato (acqua pulita dopo microfiltrazione) possiede un contenuto di sostanza secca decisamente inferiore, quasi nullo. Questo mette in luce come l’efficienza del processo di microfiltrazione sia decisamente elevata e porti ad ottenere un campione di acqua chiarificata con un contenuto di solidi sospesi pressoché trascurabile.
I risultati ottenuti dalle prove di caratterizzazione del fango di cemento in uscita dalla microfiltrazione hanno evidenziato un contenuto di umidità variabile tra 53 e 61%. Inoltre, a valle della prova di calorimetria a conduzione isotermica, non è più stata riscontrata alcuna proprietà di idratazione, neanche dopo riattivazione con materiale pozzolanico.
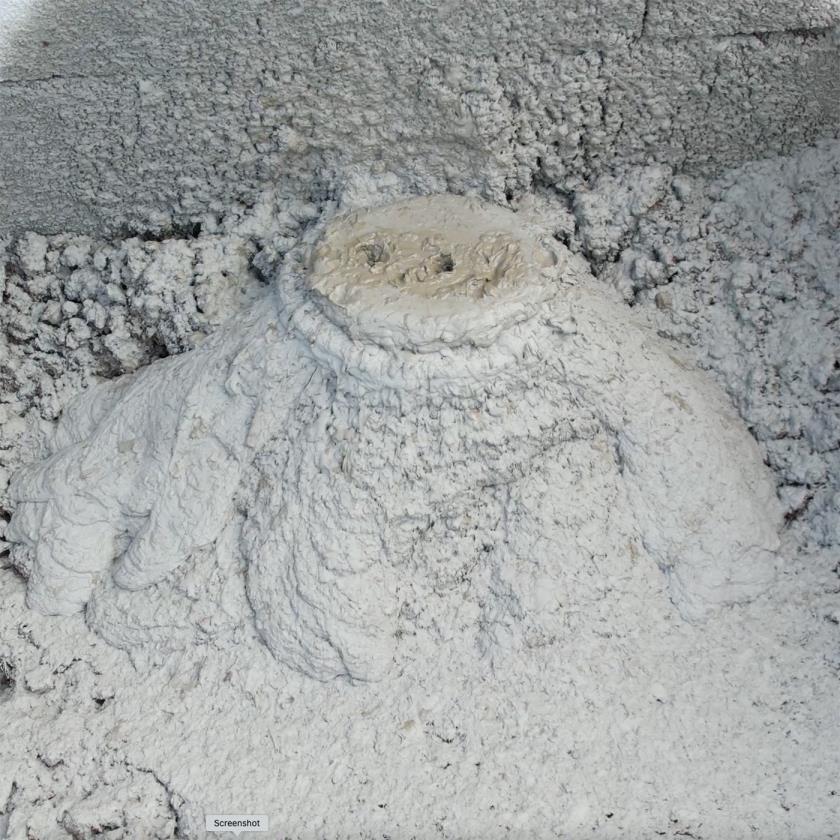
Per l’utilizzo di tale materiale nella produzione di calcestruzzo è stata pertanto valutata la fattibilità di un suo utilizzo come filler. Infine, i risultati ottenuti dalle prove di resistenza a compressione eseguite sulle miscele di calcestruzzo confezionate con l’utilizzo dei prodotti ottenuti dal trattamento del calcestruzzo reso (in diverse percentuali), hanno mostrato che, rispetto alla miscela naturale di riferimento, la miscela “50%-riciclato” presenta una riduzione di resistenza nell’intervallo 1,6 (C20/25) - 2% (C10/15 e C30/37); mentre la miscela “fango” presenta una riduzione di resistenza nell’intervallo 7,9 (C20/25 e C30/37) - 13% (C10/15).
In definitiva
Al termine delle attività di ricerca condotte è possibile affermare che tutti i prodotti ottenuti dal trattamento possono essere utilizzati per la produzione di calcestruzzo. In particolare, gli aggregati fini e grossolani sono considerati idonei alla produzione di nuovo calcestruzzo, poiché rispettano tutti i requisiti imposti dalla norma tecnica di settore UNI EN 12620.
Aggregati fini e grossolani
In regola con i requisiti imposti dalla norma tecnica di settore UNI EN 12620
Inoltre, l’utilizzo non comporta alcun impatto ambientale in termini di rilascio di possibili contaminanti. I risultati del test di cessione hanno infatti confermato il rispetto di tutti i limiti imposti dal decreto ministeriale 186/2006. Allo stesso modo, anche l’acqua microfiltrata può essere considerata idonea all’utilizzo come acqua di impasto per la produzione di nuovo calcestruzzo, nel rispetto dei limiti imposti dalla norma UNI EN 1008.
Acqua di recupero
In regola con i requisiti imposti dalla norma tecnica di settore UNI EN 1008
Il processo di microfiltrazione implementato da Wamgroup inoltre risulta essere performante. Il contenuto di solidi sospesi totali presente nell’acqua microfiltrata è, infatti, quasi nullo. Per quanto riguarda invece il fango di cemento, è stata dimostrata la fattibilità di un suo utilizzo come filler all’interno di nuove miscele di calcestruzzo. Il calcestruzzo prodotto con l’utilizzo combinato di aggregati riciclati e acqua riciclata (microfiltrata) garantisce prestazioni meccaniche pressoché simili a quelle di un calcestruzzo tradizionale. Allo stesso modo, anche l’utilizzo parziale del fango di cemento come filler (in sostituzione della sabbia naturale) permette l’ottenimento di miscele di calcestruzzo con buone prestazioni meccaniche. In particolare, è preferibile l’utilizzo per calcestruzzi ad alta resistenza, quali ad esempio C20/25 e C30/37.
Prestazioni? Ok!
Le prestazioni meccaniche dei calcestruzzi ottenuti con il reimpiego degli inerti di recupero sono allineate con quelle di calcestruzzi composti da inerti vergini
In conclusione, è possibile affermare che la tecnologia di recupero del calcestruzzo di risulta implementata da Wamgroup permette di ottenere veri e propri prodotti che possono essere immessi sul mercato e riutilizzati direttamente nella centrale di betonaggio per la produzione di nuovo calcestruzzo garantendo, contemporaneamente, adeguate prestazioni tecniche e ambientali.
Informazioni e dati contenuti nell’articolo sono tratti dalla ricerca “Direzione economia circolare: nuove opportunità dal recupero del calcestruzzo di risulta” prodotta dal dipartimento di Ingegneria civile, architettura, territorio, ambiente e di matematica dell’università di Brescia (gruppo di ricerca Alessandra Diotti, Luca Cominoli, Giovanni Plizzari, Sabrina Sorlini).